Policies
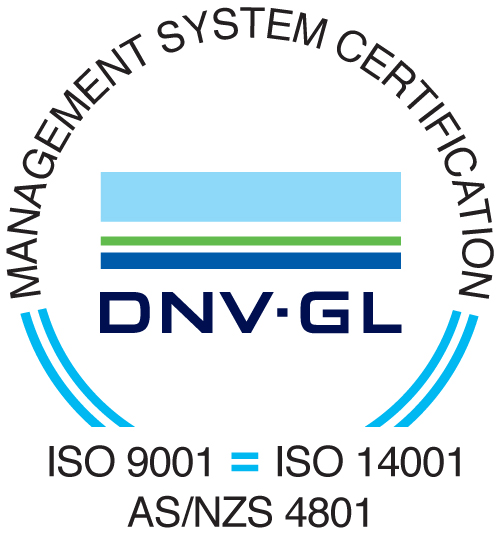
INTEGRATED MANAGEMENT SYSTEM MANUAL
This integrated management system manual describes how Extran organise our business processes and practices so that we can ensure a consistent, high quality product is delivered to suit the client’s needs. We have outlined in this manual what it is we do in order to control quality, environmental and OH&S issues in line with ISO 9001:2015 + ISO 14001:2015 + AS/NZS 4801:2001. More detail on methods used can be seen in the Nominated Procedures. This manual is subject to periodic review. This, and any subsequent revisions are approved by the IMS Manager. Revisions are identified in the revision box on the front cover.
OUR BUSINESS PROFILE AND CAPABILITIES
Extran is an Australian company determined to excel in the field of Heat Transfer Equipment, Design, Manufacture and Maintenance. The company has the ability in-house to design and manufacture complete industrial cooling and heat transfer systems with a range of heat exchanger products that includes Plate Heat Exchangers, Shell & Tube Heat Exchangers, Air Coolers, Oil Coolers, Industrial Radiators and Cooling Towers.
The directors & shareholders have combined over 80 years of experience in the heat exchanger industry. The company has the engineering depth for complex heat transfer problems and code conformance requirements and operates an Integrated Management System certified as being in accordance with ISO 9001:2015, ISO 14001:2015 & AS/NZS 4801:2001 and design capabilities include AS 1210, AS 1228, ASME [Div 1 & 2] and BS 5500.
In addition to the Heat Exchanger design and manufacturing capability our Service Workshop has highly skilled staff with many years experience in the service, re-building and repair of Heat Exchangers, Oil Coolers, Air Coolers, Plate Heat Exchangers, Shell & Tube Heat Exchangers and Industrial Radiators.
Products designed are for Industrial applications in Australian conditions of high ambients where corrosion resistance and robustness are requirements. This combination of a Heat Exchanger Manufacturing capability combined with the Heat Exchanger Service Workshop offers a unique service to clients of Extran.
QUALITY POLICY
It is the aim of Extran to be a leading provider of products and services in the Heat Transfer Industry. To ensure we meet this goal Extran run a Quality System in accordance with ISO 9001:2015. The objective of running this system is to provide our Customers with the best products and services we can. We measure our success by meeting our Customer’s expectations in terms of quality, on-time delivery and competitiveness.
The needs and satisfaction of our Customers are considered critical success factors for the company and are continually monitored and assessed.
All personnel within Extran are fully committed to and responsible for quality of product and workmanship and to upholding our quality policy as outlined in this manual. In conjunction with our Suppliers and Subcontractors, we will continue to develop our design and manufacturing capabilities in order to further improve the products and services delivered to our Customers. Working in accordance with our procedures and work instructions enhances quality in a systematic manner. Not all procedures are mentioned in this Manual, some procedures may be given to Customers upon request however there are some that are confidential as they contain ‘secrets of the trade’.
The Production Manager has the authority, responsibility and organizational freedom to identify Quality Issues, to stop or continue with work in progress, to provide solutions and to verify resolution of such issues. The Production Manager has management responsibility for technical aspects of the workshop with regard to the supervision of the work, workshop safety, training and quality issues. Further role description is detailed in the position report and relationship shown on the following chart.
The Company Director has an active interest in the quality system and the IMS manager is a senior position within the Company. Management Responsibility for Quality Management System is further explained in Procedure 1. The role of the IMS Manager is to oversee all aspects of the Quality System and have responsibility for the maintenance and implementation of the system.
ENVIRONMENTAL POLICY PREAMBLE
Extran values its commitment to environment and community responsibility. This is fundamental to the way we do business.
This will be achieved by striving to continually improve our environmental systems and practices and by comparing those against industry standards.
COMMONWEALTH & STATE LAW
The company policy is to comply with all legislation in this area enacted by the federal and state legislatures.
RESPONSIBLE OFFICER
The Company Directors are ultimately responsible for implementation and effective implementation of the company’s environmental policies and programs.
GENERAL
The company will for its part :
- Focus on reducing environmental impact in each and every one of our activities.
- Develop, implement and maintain management standards for the environment that enables it to identify, assess and manage risks to employees, visitors and the environment.
- Provide and maintain a workplace which secures a healthy environment.
- Provide information and training for all employees to ensure their understanding of environmental procedures and requirements.
- Provide effective consultation with employees on all issues which may effect the environment at work.
- Establish measurable objectives and targets to ensure continued improvement of environmental issues at our workplace.
- Provide effective reporting, recording measures for environmental issues.
- Provide effective risk management reporting, recording and review.
- Encourage recycling and the segregation of waste into recyclable and non-recyclable.
- Ensure wastewater systems are installed and maintained.
The employees for their part will :
- Actively participate in the development of environmental procedures, rules and regulations.
- Observe these environmental procedures and regulations and make proper use of available safety procedures, safety devices and personal protective equipment. In addition, complying with any reasonable instruction from a supervisor in relation to environmental issues at work.
- Through consultation, training and instruction take an active interest and commitment to the environment and community.
- Comply with all relevant federal and state laws to provide a safe and healthy workplace for yourself, fellow employees and visitors to Extran and our environment.
- Segregate waste into recyclable and non-recyclable and dispose of accordingly.
- Make every effort to reduce waste and protect the environment.
The company’s directors and employees will endeavour to reach consensus on all aspects of the company’s environmental policy and program through the process of joint consultation.
Any person in our company who would like to discuss a matter pertaining to our workplace environment can do directly with their manager or any of the company directors.
OCCUPATIONAL HEALTH & SAFETY POLICY
It is the policy of Extran to work with its employees to promote good health and safety practice and provide sufficient resources in order that those things, which cause workplace accidents and ill health, may be eliminated and so that together, we can fulfil our responsibilities under occupational health and safety legislation and therefore provide a safe environment for our employees, visitors, contractors and public by;
- Providing and maintaining a safe place of work.
- Providing and maintaining safe plant and equipment.
- Ensuring the safe handling, use and storage of substances.
- Providing adequate control of the health and safety risks arising from the activities involved in the manufacture and maintenance of heat transfer equipment.
- Providing such information, instruction and supervision necessary to secure their safety and health at work and that of others who may be affected by their actions.
- Consulting employees on matters affecting their health and safety.
- Carrying out health surveillance, where required.
- Monitoring safety performance to maintain agreed standards.
- Reviewing and revising this policy as necessary at regular intervals.
- At all times acting in an ethical manner with integrity and honesty.
RESPONSIBILITIES
The following health and safety responsibilities are assigned to the persons in this section.
The Directors
The directors have overall responsibility for health and safety within the workplace.
Specifically, the directors will;
a) Ensure that this policy is brought to the attention of, and implemented by, every employee;
b) Monitor the effectiveness of this policy in reducing workplace accidents and ill health;
c) From time to time, review and as necessary, revise this OHS policy and bring such revisions to the attention of all employees;
d) Ensure that adequate resources in terms of time, finance, personnel and equipment are made available so as to ensure the health, safety and welfare of employees;
e) Arrange for the undertaking of a programme of risk assessments for the purposes of identifying;
- The risks to which employees are exposed;
- The risks to which persons other than employees are exposed;
- The measures necessary to eliminate or reduce the risks identified by the assessment.
f) Ensure the development of safe systems of work;
g) Ensure the development of procedures to deal with emergencies;
h) Ensure the development of procedures for investigating accidents, near misses, dangerous occurrences and cases of work related ill health;
i) Ensure that all work equipment is in good repair and in good condition and fit for use;
j) Provide such information and training to employees so as to ensure their health and safety at work;
k) Ensure the provision and maintenance of adequate welfare facilities for employees;
l) Arrange for all accidents, near misses, dangerous occurrences and cases of work related ill health to be reported to the Directors.
The directors may delegate the execution of some of their duties under this policy to a suitably competent employee.
Production Manager & Supervisor
The Production Manager & Supervisor have responsibility for the day-to-day management of health and safety within the workshop.
Specifically, they will;
a) Ensure that employees under their control undertake their work and use any equipment or substance in accordance with the training and information that they received;
b) Regularly inspect their area of work and the work equipment under their control and bring any defects to the immediate attention of the Director;
c) Encourage each employee under their control to behave in a safe manner by setting a good example;
d) Coordinate and monitor fire protection.
e) Report to the Business Operations Manager and/or Directors all accidents, near misses, dangerous occurrences and cases of work related ill health.
f) Assist and advise in the undertaking of risk assessments;
g) Provide information arising from risk assessments for management review meetings;
h) Ensure workshop equipment is regularly tested and testing recorded;
i) Investigate all accidents, near misses, dangerous occurrences and cases of work related ill health and report to the management review meeting.
Business Operations Manager
The Business Operations Manager is to assist the Directors in complying with health and safety legal obligations and to promote best practice standards in health and safety within the company.
This manager will;
a) Coordinate company health and safety with the assistance of the Work Shop Manager and Supervisor.
b) Nominate the Health and Safety Officer.
c) Assist and advise in the undertaking of risk assessments;
d) Assist and advise in the development of safe systems of work;
e) Provide advice and information on health and safety to all staff;
f) Organise periodic audits and report findings to the Director/s.
Employees
Every employee will;
a) Take reasonable care for their own safety and the safety of anyone else who might be affected by their acts or omissions;
b) Take reasonable care of work equipment and promptly report any defect to their manager or supervisor;
c) Make full and proper use of anything provided by their employer in the interests of health and safety (including personal protection equipment);
d) Undertake work strictly in accordance with the instruction, procedures and training provided.
e) Report all accidents, near misses, dangerous occurrences and cases of work related illness to their Supervisor;
f) Co-operate with their employer in matters of health and safety;
g) Familiarise themselves with this policy.
In addition, no employee shall;
a) Interfere with, nor misuse anything provided in the interests of health and safety;
b) Carry out any work unless it is in accordance with a procedure or;
c) Undertake any task for which they have not been authorised and for which they are not adequately trained.